Modelling the As-cast Structure in Large Steel Casting
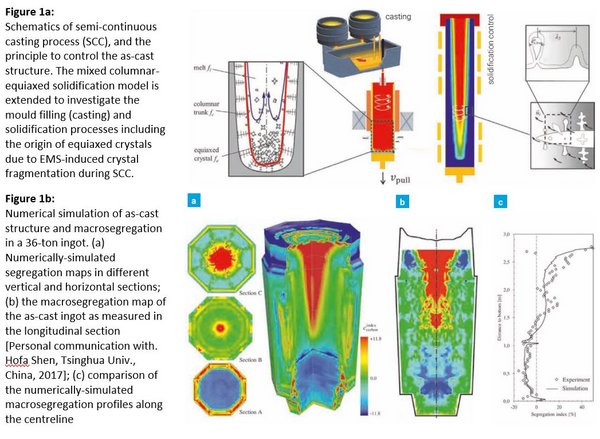
An industrial steel casting might easily weigh from a few kilograms up to a few hundred tons. They can be cast either as conventional ingots or poured continuously to form slabs or billets. Typical as-cast structures are presented in the form of columnar or equiaxed crystals, but mostly in the form of mixed columnar and equiaxed. Due to the large tonnage, the castings may take days or weeks to solidify. Different transport phenomena occur, e.g. crystal motion and melt convection, which lead to heterogeneity of the as-cast structure and alloy composition. Understanding these phenomena is of our key interest.
This research has the potential to control the as-cast structure and minimize the macrosegregation in industry castings (ingots and continuous casting of steel, DC casting of non-ferrous alloys) by optimizing the casting parameters. It may aid industry to design new solidification processes (e.g. semi-continuous casting of steel). A smart model allows an integration into industry 4.0 as an important tool for the virtual/intelligent manufacturing.
The primary aims and objectives of this research topic are:
- To understand the formation of the as-cast structure of steel castings that are manufactured at an industrial scale;
- To develop a numerical model for the mixed columnar-equiaxed solidification considering columnar-to-equiaxed-transition (CET) and macrosegregation;
- To model the electromagnetic stirring during continuous casting, and its effect on the as-cast structure (crystal fragmentation);
- To apply the numerical model to aid industry to optimize the casting processes (ingot, continuous casting);
- To apply the numerical model to aid industry to design a new casting process (semi-continuous casting);
- To further evaluate the numerical model by comparing the modelling results with laboratory experiments and plant trials.
Examples of recent achievements are given in Fig. 1. Further details on that topic can be found in
- Zhang H. Liu X., Ma D., Ludwig A., Kharicha A., Wu M.: IOP Conf. Series: Mater. Sci. Eng. 1274 (2023) 012026. DOI: 10.1088/1757-899X71274/1/012026
"Potential eutectic accumulation in single crystal turbine blade due to geometry effect: a numerical study" - Zhang Z., Wu M., Zhang H., Ludwig A., Kharicha A.: Steel Research int. (2022). DOI: 10.1002/srin.202200065
"The Role of Mold Electromagnetic Stirring in the Dissipation of Superheat during the Continuous Casting of Billets" - Zhang H., Wu M., Zhang Z., Ludwig A., Kharicha A., Ronaföldi A., Roosz A., Veres Z., Sveda M.: Metall. Mater. Trans. B (2022). DOI: doi.org/10.1007/s11663-022-02516-3
"Experimental Evaluation of MHD Modeling of EMS During Continuous Casting" - Wu M., Stefan-Kharicha M., Kharicha A., Ludwig A.: Int. J. Heat and Mass Trans. 164 (2021) 120566. DOI: 10.1016/j.ijheatmasstransfer.2020.120566
"Flow-solidification interaction: A numerical study on solidification of NH 4 Cl –70 wt.%H 2 O solution in a water-cooled mould with a large sample thickness" - Zhang H., Wu M., Tewari S.N., Ludwig A., Kharicha A.: J. Mat. Proc. Tech. 288 (2021) 116913. DOI: 10.1016/j.jmatprotec.2020.116913
"Geometrical effect on macrosegregation formation during unidirectional solidification of Al–Si alloy" - Zhang H., Wu M., Zhang Z., Ludwig A., Kharicha A.: MCWASP XV, IOP Conf. Series: Mater. Sci. Eng. 861 (2020) 012048. DOI: 10.1088/1757-899X/861/1/012048
"Influence of crystal fragmentation on the formation of microstructure and macrosegregation during directional solidification under forced convection condition" - Wu M., Stefan-Kharicha M., Kharicha A., Ludwig A.: MCWASP XV, IOP Conf. Series: Mater. Sci. Eng. 861 (2020) 012041. DOI: 10.1088/1757-899X/861/1/012041
"Numerical investigation of an in-situ observed flow regimes during solidification of an NH 4Cl - 70wt%H 2O solution" - Zhang Z., Wu M., Zhang H., Karimi-Sibaki E., Ludwig A., Kharicha A.: MCWASP XV, IOP Conf. Series: Mater. Sci. Eng. 861 (2020) 012024. DOI:10.1088/1757-899X/861/1/012024
"Modeling mixed columnar-equiaxed solificiation of Sn-10wt% alloy under forced convection driven by travelling magnetic stirring" - Zhang H., Wu M., Zhang Y., Ludwig A., Kharicha A.: Mat. Today Comm. 22 (2020) 100842. DOI: 10.1016/j.mtcomm.2019.100842
"Numerical study of the role of mush permeability in the solidifying mushy zone under forced convection" - Wu M., Ludwig A., Kharicha A.: Metals 9 (2019) 229 1-43. DOI: 10.3390/met9020229
"Volume-Averaged Modeling of Multiphase Flow Phenomena during Alloy Solidification" - Wu M., Ludwig A., Kharicha A.: Steel Res. Int. 89 (2018) 1700037 1-14. DOI: 10.1002/srin.201700037
"Simulation of As-Cast Steel Ingots" - Y. Zheng, M. Wu, A. Kharicha, A. Ludwig: China Symposium on Sustainable Steelmaking Technology, Oct. 24-26, 2018, Tianjin, China, Proceedings in electric device: 355-357
“Concept of semi-continuous casting (SCC) for large steel strand: a numerical study” - Zheng Y., Wu M., Kharicha A., Ludwig A.: Modelling Simul. Mater. Sci. Eng. 26 (2018) 015004 1-18. DOI: 10.1088/1361-. 651X/aa86c5
"Incorporation of fragmentation into a volume average solidification model" - Wu M., Ludwig A., Kharicha A.: Appl. Math. Modelling, 41 (2017) 102-20.
"A four phase model for the macrosegregation and shrinkage cavity during solidification of steel ingot" - M. Wu, Y. Zheng, A. Kharicha, A. Ludwig: , 7th Int. Conf. on Mod. & Simul. of Metall. Processes in Steelmaking (STEELSIM2017), Qingdao, China, 129-32.
“Numerical analysis of as-cast structure, macrosegregation and shrinkage cavity in steel ingots: case study of a 36 tons’ ingot” - Ludwig A., Wu M., Kharicha A.: Metall. Mater. Trans. A, 46 (2015) 4854-4867.
"On Macrosegregation" - Li J., Wu M., Ludwig A., Kharicha A.: Int. J. Heat and Mass Transfer 72 (2014) 668-679.
"Simulation of Macrosegregation in a 2.45-ton Steel Ingot Using a Three-Phase Mixed Columnar-Equiaxed Model"
see also our Topic Related Publications