Formation Mechanism of Macrosegregation
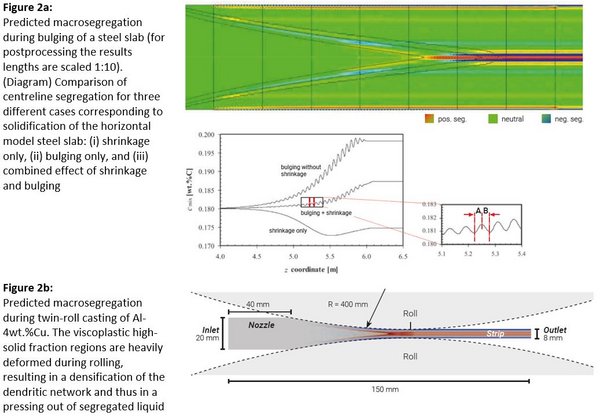
The compositional heterogeneity at the scale of industry casting is called macrosegregation. It is caused by the fact that usually solidifying crystals do not incorporate all alloying elements and thus the remaining melt gets enriched in solute, leading to so-called (micro-)segregation. If the flow transports this solute-enriched melt elsewhere, the composition in the casting becomes heterogeneous. As there are many mechanisms leading to a relative movement between crystal and liquid (e.g. thermal or solutal buoyancy, sedimentation, deformation, etc.), macrosegregation can easily occur. One may also think that measures, to be taken to control its formation, are numerous as well. However, the measures must be smart enough.
This research topic has the potential to extend our understanding of macrosegregation formation, to develop industrial relevant strategies for minimizing macrosegregation. The refined solidification models (source codes) can be integrated into industry 4.0 as an important tool for virtual/intelligent manufacturing.
The primary aims and objectives of this research field are:
- to use multiphase solidification models and to study macrosegregation mechanisms as caused by: - thermo-solutal convection; - crystal sedimentation; - feeding flow due to solidification shrinkage; - forced flow such as electro-magnetic stirring; - mechanical deformation of the mushy zone; - Marangoni convection.
- to evaluate numerical models against different theoretical models or experimental benchmarks: - laboratory experiments; - Flemings theory; - industry castings.
- to apply numerical models for different industry processes (ingots, continuous castings of steel, and direct chill casting of copper/aluminium).
Examples of recent achievements are given in Fig. 2. Further details on that research field can be found in:
- Zhang Z., Wu M., Zhang H., Ludwig A., Kharicha A.: Inter. J. Heat and Mass Trans. 208 (2023) DOI: doi.org/10.1016/j.ijheatmasstransfer.2023.124050
"Effect of forced convection on the formation of the as-cast structure and macrosegregation of Sn-10wt.% Pb alloy: A numerical study" - Zhang H., Liu X., Ma D., Song M., Ludwig A., Kharicha A., Wu M.: Acta Materialia 244 (2023) DOI: doi.org/10.1016/j.actamat.2022.118579
"Digital twin for directional solidification of a single-crystal turbine blade" - Guan R., Rodrigues C.M.G., ji C., Zhu M., li S., Wu M., Kharicha A., Vakhrushev A., Ludwig A.: App. Math. Modelling 114 (2023) 770-784 DOI: doi.org/10.1016/j.apm.2022.10.025
"Novel strategy to model deformation-induced strand contraction/dilatation during mechanical reduction" - Zhang H., Wu M., Rodrigues C.M.G, Ludwig A., Kharicha A., Rónaföldi A., Roòsz A., Veres Z., Sveda M.: Acta Materialia 241 (2022) DOI: doi.org/10.1016/j.actamat.2022.118391
"Dendrite fragmentation mechanism under forced convection condition by rotating magnetic field during unidirectional solidification of AlSi7 alloy" - Rodrigues C.M.G., Wu M., Zhang H., Ludwig A., Kharicha A.: Materialia 23 (2022). DOI: doi.org/10.1016/j.mtla.2022.101462
"Validation of a capillary-driven fragmentation model during mixed columnar-equiaxed solidification with melt convection and grain transport" - Stefan-Kharicha M., Kharicha A., Zaidat, K., Reiss G., Eßl X., Goodwin F., Wu M., Ludwig A., Mugrauer C.: J. Crystal Growth 584 (2022) 126557. DOI: doi.org/10.1016/j.jcrysgro.2022.126557
"Hydrodynamically driven facet kinetics in crystal growth" - Zhang Z., Wu M., Zhang H., Hahn S., Wimmer F., Ludwig A., Kharicha A.: J. Mat. Proc. Tech. 301 (2022). DOI: 10.1016/j.jmatprotec.2021.117434
"Modeling of the as-cast structure and macrosegregation in the continuous casting of a steel billet: Effect of M-EMS" - Rodrigues C., Wu M., Zhang H., Ludwig A., Kharicha A.: Metall. Mater. Trans. A (2021). DOI: 10.1007/s11661-021-06414-2
"Bridging Capillary-Driven Fragmentation and Grain Transport with Mixed Columnar-EquiaxedSolidification" - Zhang H., Wu M., Rodrigues C., Ludwig A., Kharicha A.: Metall. Mater. Trans A (2021). DOI: 10.1007/s11661-021-06295-5
"Directional Solidification of AlSi7Fe1 Alloy UnderForced Flow Conditions: Effect of Intermetallic Phase Precipitation and Dendrite Coarsening" - Zhang H., Wu M., Schumacher P., Rodrigues C., Ludwig A., Kharicha A.: Appl. Math. 97 (2021) 821- 838. DOI: 10.1016/j.apm.2021.04.024
"Modelling melting and grain destruction phenomena during globular equiaxed solidification" - Rodrigues C., Ludwig A., Wu M., Kharicha A., Vakhrushev A.: J. Mat. Proc. Tech. 286 (2020) DOI:10.1016/j.jmatprotec.2020.116814
"Two-phase viscoplastic model for the simulation of twin roll casting" - Rodrigues C., Ludwig A., Wu M., Kharicha A., Vakhrushev A.: Metall. Mater. Trans. B 50 (2019) 1334-1350. DOI: 10.1007/s11663-019-01527-x
"A Comprehensive Analysis of Macrosegregation Formation During Twin- Roll Casting" - Wu M., Ludwig A., Kharicha A.: Steel Res. Int. 89 (2018) 1700037 1-14. DOI: 10.1002/srin.201700037
"Simulation of As-Cast Steel Ingots" - Zheng Y., Wu M., Karimi-Sibaki E., Kharicha A., Ludwig A.: Int. J. Heat and Mass Trans. 122 (2018) 939–953. DOI: 10.1016/j.ijheatmasstransfer.2018.02.012
"Use of a mixed columnar-equiaxed solidification model to analyse the formation of as-cast structure and macrosegregation in a Sn-10 wt% Pb benchmark experiment" - Rodrigues C., Ludwig A., Kharicha A., Wu M.: Trans. Indian Inst. Met. 71 (2018) 2645-2649. DOI: 10.1007/s12666-018-1423-8
"Modeling of the Twin-Roll casting Process: Transition from Casting to Rolling" - Wu M., Zeng Y., Kharicha A., Ludwig A.: Comp. Mater. Sci. 124 (2016) 444-55.
"Numerical analysis of macrosegregation in vertically solidified Pb-Sn test castings - Part I: Columnar solidification." - Zheng Y., Wu M., Kharicha A., Ludwig A.: Comp. Mater. Sci. 124 (2016) 456-70.
"Numerical analysis of macrosegregation in vertically solidified Pb-Sn test castings – Part II : Equiaxed solidification" - Ahmadein M., Wu M., Ludwig A.: J. Crystal Growth 417 (2015) 65-74.
"Analysis of macrosegregation formation and columnar-to-equiaxed transition during solidification of Al-4wt.%Cu ingot using a 5-phase model" - Domitner J., Wu M., Kharicha A., Ludwig A., Kaufmann B., Reiter J., Schaden T.: Metall. Mater. Trans. A, 45 (2014) 1415-1434.
"Modeling the effect of strand surface bulging and mechanical softreduction on the macrosegregation formation in steel continuous casting" - Wu M., Domitner J., Ludwig A.: Metall. Mater. Trans. A, 43(2012) 945-964.
"Using a two-phase columnar solidification model to study the principle of mechanical softreduction in slab casting”
see also our Topic Related Publications